Our companies do very similar things. The team of Primority drives digital food supply chains into food businesses to help them protect the consumer, comply with regulations and retail standards. Solutions like their 3iVerify software ultimately aim to reduce the risk and cost of food recall and withdrawal. They recently announced that they are launching a new software service called AI Scan that scans risk events like import alert & refusals, product recalls and negative news coverage. This is very similar to one of the modules of our food safety intelligence platform.
In this article, I am interviewing James Flynn, the CTO and Founder of Primority Ltd. He is a science and software technology graduate with almost 30 years’ experience in food safety management systems. His bio says that he pioneered HACCP software in the mid 1990’s and has helped thousands of food businesses document their food safety systems.
So is James, a competitor?
Looking more closely at Primority, I see that we are not serving the same audience and that we are targeting different market segments. We both believe in the power of digital transformation for food quality and safety. We are both on the same mission – to ensure safe food for everyone by helping food industry professionals adopt the right digital tools. We both utilize content marketing to position our companies as thought leaders and share with our partners and clients what we learn at work.
Furthermore, Primority is headquartered in Kirkcaldy, Scotland. The “Lang Toun” linoleum capital of the world, known as the birthplace of social philosopher and economist Adam Smith who wrote his magnum opus The Wealth of Nations in the town.
So James is offering a complementary solution, is part of a dynamic team, and is based in a historic town. What could be more inspiring for an interview?
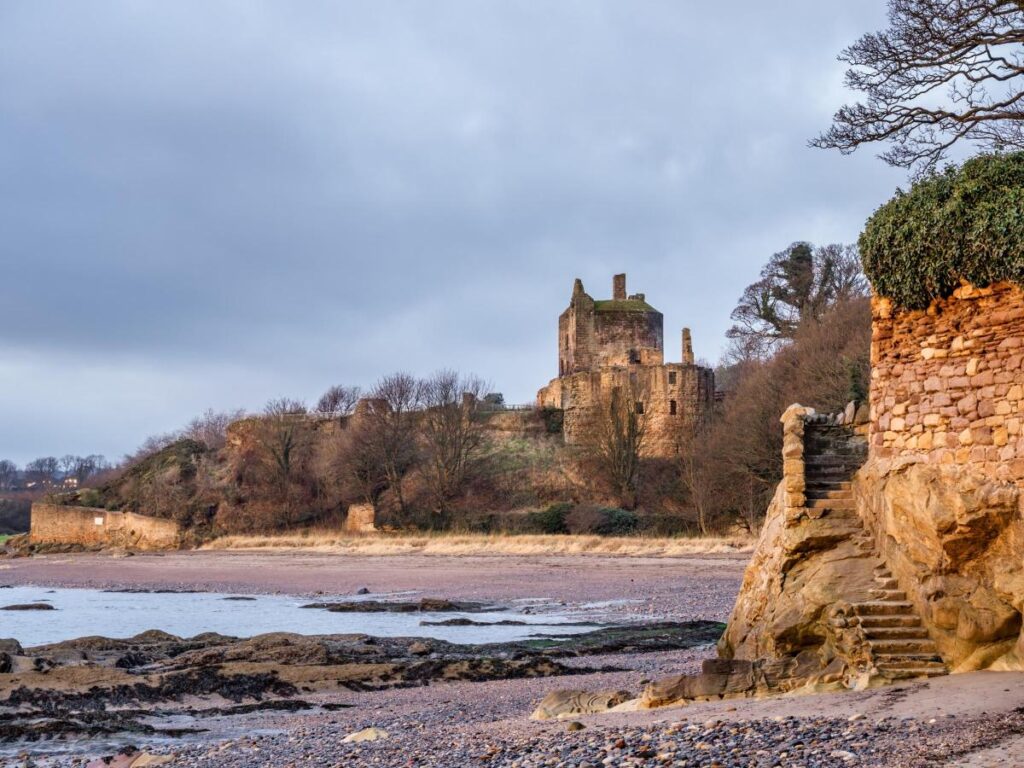
(Photo courtesy The National, from https://www.thenational.scot/news/17792362.scotland-39-s-insider-guide-kirkcaldy/)
James, what is your opinion? Which changes do you see coming in the market?
COVID-19 has taught the world, at pace, how to ‘go digital’. It has been a driver of necessity. This means that more people than ever are now more savvy when it comes to using technology to communicate. Even something as simple as Zoom, which most consumers did not know about before COVID-19, has evolved rapidly to become the so called ‘new normal’ in how professionals and consumers alike can communicate effectively. The latent stigma from before of appearing on camera has largely evaporated as people cast aside their inhibitions because they have to do so.
Therefore, I expect that there will be a positive effect on the adoption of other digital technologies in the work place. There will be less friction of adoption to using technology to do jobs that needed a face to face interaction in the past (like audits and inspections). It is clear to all now that many common tasks, e.g. weekly meetings, can easily be augmented with the use of remote technology that is not only ‘COVID secure’, as UK government phrases it, but is more productive because of reduced travel times and is better for the planet.
Assuming this is the case, I think we can expect to see a wider adoption of more digital technologies that help save time, reduce costs (businesses will need to reduce their costs to recover their capital where they can) and also reduce risks, COVID, Food Safety, Food Fraud.
I also believe that we will see an acceleration in the use of blockchains and digital ledgers as these technologies can bring much more efficient methods of sharing food supply chain information and, again, help reduce information friction costs.
What do you hear from your clients? Which needs are they highlighting during this period?
The experience of working with our clients during the COVID-19 pandemic has been very interesting. The lockdown and resultant remote working of many of our contacts in manufacturing has led to them having the time to look at new projects. Many of them have now implemented new areas of our solution because they have had the time and space, without the normal interruption of day to day life in the office.
This has highlighted that managers actually can manage many tasks better when they are working from home, especially when working on new initiatives. The result is that several of our customers have moved further along in their digitisation journey, moving from just doing cloud based supplier and raw material management for example. Now they are implementing digital corrective actions, digital document management and also adopting and starting to use our AI Scan platform for supplier surveillance.
How do you respond to these needs? What is your company doing differently to serve your clients better?
We have responded to the needs of our clients by doing what we always do, and that is spending the time to work with them to improve what our 3iVerify solution does for them. Every day, we discuss our solution with clients to take feedback on board and plan in the elements which are important to our clients into our solution.
For us, the best thing we can do for our clients is to listen, plan, and then implement what they require. Mostly, these are small, incremental improvements and we work on that every day. However, we have longer term improvements, such as AI Scan, which take a lot more development, testing and feedback and this is where a huge amount of effort is happening for us at present.
We believe that the AI Scan module of our solution is a game changer in that it provides information on a very common blind spot in the food supply chain, i.e. how do suppliers perform between audits and certification periods? We want to help our clients by automating the mammoth task of checking that suppliers are providing high quality, safe and legal food materials and by alerting them to food safety and other risks that they might not otherwise be aware of.
In your opinion, what is the digital technology that will be more extensively adopted by the market during the next 12 months?
I believe that we will see more remote inspection technology, perhaps smart glass technology, in use to work more closely with suppliers, more often. I also believe that digitising food safety and quality management is now much higher up the agenda of industry in general because they have learned more about how technology can help them.
Many of our customers were only able to work from home because they have 3iVerify and this has demonstrated very effectively the benefits of a cloud based portal in a way that I never imagined before. Therefore, it is my hope that the benefits of cloud technology have become a lot more clear and ultimately this leads to digital ledger technology being more adopted by the food sector.
Video conferencing is the other big change that will positively impact how we work together in general. This will open up greater collaboration between our customers and their suppliers as well as between our customers and us (although in truth, ALL of our customers have been onboarded to this way of working with us for years already).
If you wish to receive updates on similar interviews from people like James, feel free to subscribe below.