Let’s talk about food risk assessment.
The process through which food safety or supplier compliance teams need to calculate a risk indicator for thousands of ingredients and hundreds of suppliers, so that they rank them in terms of priority and vulnerability.
A calculation that can be done using some widely accepted risk assessment formulas or an internal risk scoring model. But also a process that may take days, very often weeks – and, in some cases, months.
Also a process that is usually taking place using an Excel spreadsheet that collects and combines tons of different data inputs. Many companies opt for a software tool that may automate parts of this calculation, such as Registrar Corp’s FDA Compliance Monitor, FERA’s Horizon Scan, and Primority’s AI Scan.
Still, the challenge remains: the calculation of a risk score for each and every ingredient and supplier can become an extremely time-consuming and difficult task.
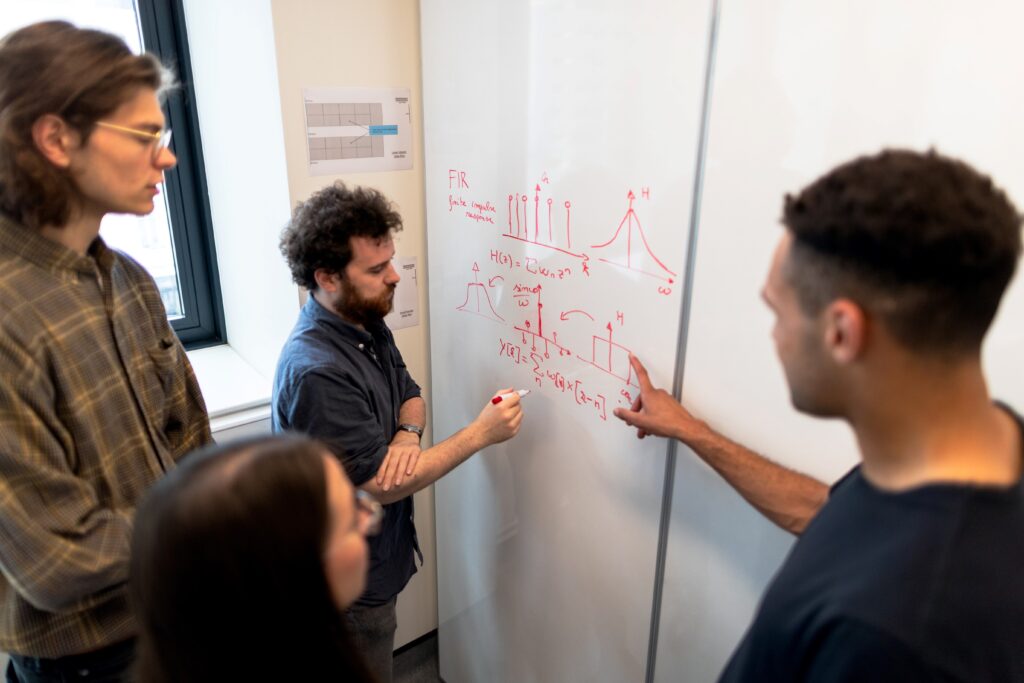
(Photo by ThisisEngineering RAEng on Unsplash)
The inherent complexity of risk assessment and ranking is that it needs to take into consideration multiple dimensions that contribute to the overall risk score – and therefore, combine numerous data inputs. As a matter of fact, people working at ingredient and supplier assessment roles, very often need to combine heterogeneous information that comes from several sources and people, both internally and externally:
- numbers of incidents reported globally for a key ingredient or supplier
- what internal lab testing results show about key ingredient categories
- risks that have been emerging in the market
- supplier performance in recent audits
- supplier compliance to required certification schemes
- internal and external expert opinions
…and the list goes on.
So how can AI and predictive technologies change the traditional ways in which systematic risk assessment and ranking is taking place?
Let me walk you through some of the options.
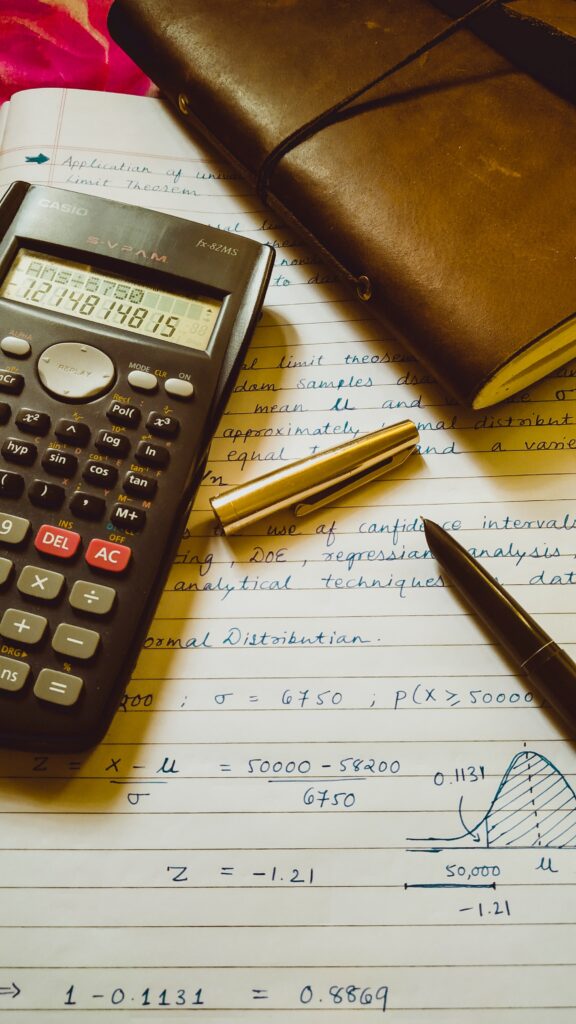
(Photo by Vishwarajsinh Rana on Unsplash)
Option 1: Rely upon your team’s experience and ability to assess and prioritize risks related to your ingredients and suppliersÂ
No spreadsheet. No risk models. Trust the experience and intuition of your team that knows best about the risks that should be expected and prevented.
Assumes that you fully trust your team and that they have solid understanding and knowledge of both known and unknown risks that might emerge in your supply chain.
Option 2: Bring external experts on board to contribute to the conversation about risks the company should be focusing on
A routine followed by many companies out there. For instance, they organize a risk assessment and prioritization meeting every six or twelve months, in which external experts and their team members discuss which risks the company should be prepared for.
Assumes that you feel confident that nothing urgent will occur between these meetings. Also that the experts that you bring around the table can offer reliable advice and insights.
Option 3: Use a periodically updated spreadsheet to combine data inputs and calculate a risk score
One step closer to digital automation, can be used complementary to one of the previous options. Puts together various data inputs in order to calculate a risk score. Then, uses this risk scoring system to rank and prioritize ingredients and suppliers that are more susceptible to risk.
Assumes that you have chosen a risk assessment model that is reliable but also practical: data entry should be easy for all people contributing; and risk score calculation should be automated and straightforward.
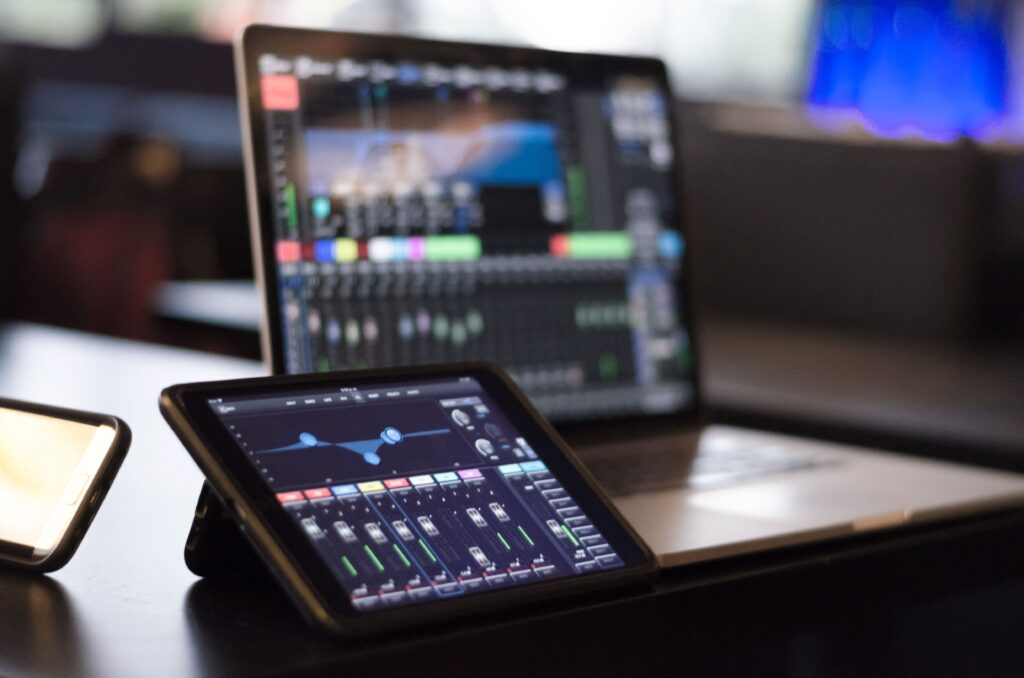
(Photo by Frederick Medina on Unsplash)
Option 4: Use a 3rd party service that automatically combines various data inputs to calculate and predict the risk score of ingredients and suppliers
Simplifies the process and makes it more dynamic. There are not so many risk assessment solutions out there, but the ones available are quite robust. Most of these tools take into consideration the numbers of incidents reported by major official sources. Then, they apply an internal risk scoring formula to assess and rank ingredients or suppliers. In some cases, a predictive algorithm is also used to incorporate expected risks in the calculation.
Assumes that you feel comfortable with the risk assessment model that the 3rd party solution uses, as customization is difficult. Relies heavily upon the number of data sources that each solution covers, therefore may not be as granular or specific as you need. Integrating data from other internal systems may also be not supported.
Option 5: Develop an internal software that automatically combines various data inputs to calculate and predict the risk score of ingredients and suppliers
Sounds like the ideal solution, but does require significant resources, senior management buy-in, and an overarching digital agenda.
An internal system makes integration with other relevant software (such as supplier performance) much easier. It also allows hard-wiring your preferred risk assessment models in the calculation process. Expanding it with AI capabilities can add cool features like processing internal audit reports to early detect emerging issues.
Assumes that you have the necessary IT resources to develop, maintain and evolve it.
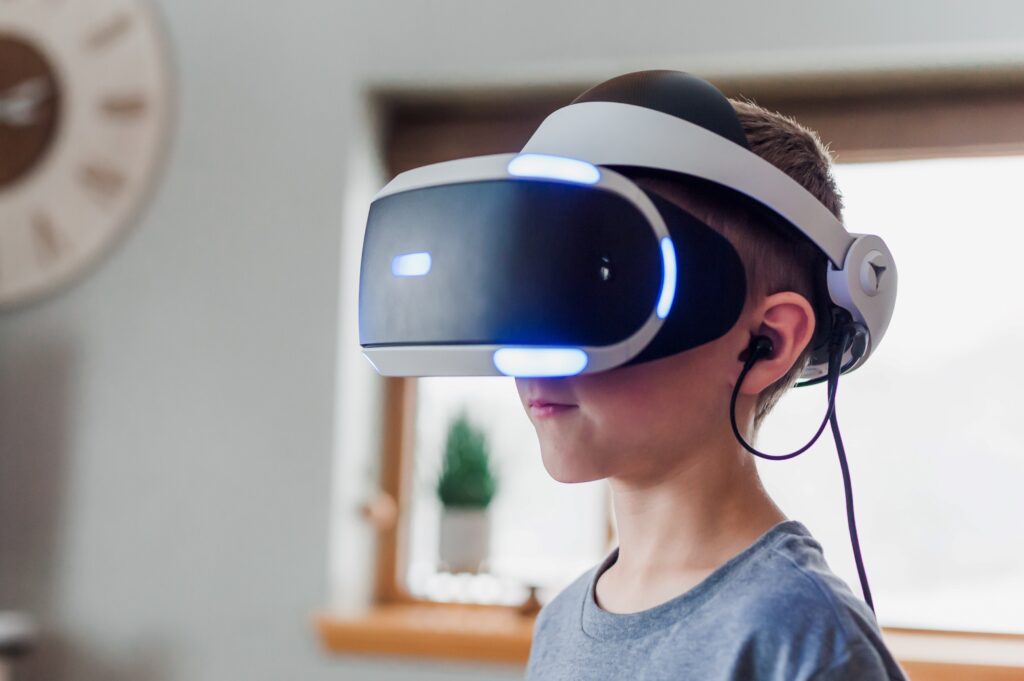
(Photo by Jessica Lewis on Unsplash)
So, looking at the software systems that automate ingredient & supplier risk assessment, which are some ways in which AI & predictive analytics can make them more powerful?
Let me use a couple of examples of the way that we do it in FOODAKAI:
(1) At supplier risk calculation
- Web site crawling software can identify, gather and incorporate in the risk model incidents reported globally about your suppliers, in near real time
- Deduplication algorithms can ensure that risk calculations do not unfairly penalize a supplier if the same incident is reported multiple times in different sources
- Natural language processing algorithms may process supplier audit reports to detect and highlight potential risks that have been documented in an automatic way
(2) At ingredient risk scoring
- Web site crawling software can identify, gather and incorporate accurately in the risk model the number of incidents that are being reported globally about key ingredients and ingredient categories
- Prediction models can estimate how many incidents per product or ingredient category are also expected in the upcoming weeks or months, incorporating this number into the risk model
- AI models may also calculate the estimated probability of hazards typically associated with key ingredients, enhancing the risk assessment model with an additional weighting factor
Which are only a few of the many ways in which AI-powered technologies can significantly expand the capabilities of software systems that support risk assessment and ranking decisions.
There is a very simple way to assess where a company stands in terms of ingredient and supplier risk assessment: use this online self-assessment tool.