I was really looking forward to talk to the person that made this statement about big data:
“I like the idea that you can use some kind of tool to interrogate information to give you the real time picture of food safety in your dashboard, whenever you want.
However, I am not sure how that works, or indeed what big data actually is… but I strongly believe it doesn’t really matter.
What I want to know is – how to use it.”
John Carter is Area Europe Quality Director at Ferrero. He has a degree in Chemical Engineering from London South Bank University, an MBA from Cambridge University, and recently completed a qualification in Business Sustainability Leadership, also from Cambridge. Prior to Ferrero, he has served in other positions at Danone, Metro Cash and Carry, Kraft Foods/Mondelez, and Campden BRI.
A globally recognised senior leader in consumer goods safety and quality, John has executive level technical leadership experience in both major retailers and manufacturers – and is currently leading the Ferrero‘s European Quality agenda. As a former board member of the Global Food Safety Initiative (GFSI), he has a track record of driving cultural change in complex, multi-national environments and has deep category experience in confectionery, dairy, plant-based foods, beverages and many other sectors. Wherever he has worked in the last thirty years he has been a champion of pragmatic risk assessment and management, enabling fast decision making and driving innovation.
It was a pleasure that he gladly accepted to share his view on the way that the epidemic is changing the food safety world. While I was expecting a discussion around his Qualicopter concept and why the function of a food safety and quality leader is “the best job in the world”, this interview ended up into becoming an almost philosophical reflection about the future of work.
Not to forget: in his first e-mail, he opened with “Efcharisto” (Thank you, in Greek) and closed with “Me tis kaliteres efxes” (Best wishes).
Philosophy and Greek words? There must be some Greek roots in the Carter family.
John, many people believe that COVID-19 accelerates the digital transformation of the food supply chain. What is your opinion? Which changes do you see coming in your work after COVID-19?
The production of food defines our world. The effects of agriculture on our daily lives are so omnipresent that they can be easy to overlook; landscapes and societies are profoundly influenced by the need to feed our growing population. But much has been taken for granted. Only occasionally are we forced to consider: “where does our food come from?”.
This has recently been accentuated by the COVID-19 crisis. The global pandemic forced populations into lockdown, and the social effects have been manifold; indeed much may not yet be apparent. The economic activity of our society shrank to its essentials. Healthcare professionals, of course, were deemed ‘frontline workers’… but the food industry too stepped up and delivered. Farms and factories around the world maintained operations and continued to fulfill obligations to their supply chains. Retailers adjusted their practices to minimise risk but ensure a safe, continuing food supply to their customers. Consumer behaviour changed, focusing initially on pantry loading with trusted staples and, later, on home food preparation (as the Horeca sector struggled).
In this context, technology has played an important role in enabling business continuity in a new reality.
Some of the changes to the ways of working have been common to all industries; the switch to remote working was sudden and forced, but teams quickly adapted thanks to the ease of use of virtual meeting technology. The food industry, being so ‘traditional’ is often one of the slowest to adopt new trends, so this crisis in fact enabled a step change in practices and indeed culture. This embrace of the possibilities of remote working will have ramifications after the crisis.
So,we have updated both our technology and our attitudes to the possibilities of remote working. The tech part has been quite smooth; the cultural aspect has been interesting… this necessitated a new discipline of communication and transparency which, coupled with a sense of solidarity against a common foe (the virus, not the auditors!) engendered a strong team spirit.
Which are the tasks that seem to be requiring the use of more digital tools and technologies?
The adoption of face-to-face video communications has enabled regular visibility between corporate central teams and factories. Decision making was necessarily swift during the crisis, and discipline coupled with a pragmatic will to make things happen allowed companies to do the right thing – quickly. This was formally enabled by the ability to use online signatures in derogation and non-conformance management (e.g. docusign). Days before the lockdown, we were still physically printing, signing and scanning such documents. Now the process is much quicker and indeed more disciplined and robust.
Video communications as a technology was also transferred to the quality audit process. A total ban on non-essential travel required auditors and auditees to adjust to the new tech; and adjust they did. Again, goodwill and trust on both sides has allowed high quality audit reports to be prepared (on reading them, most people would be unable to distinguish between a remote or a physical audit).
A physical audit will probably always be necessary in some form, at some frequency, but is fair to say that the virtual alternative is now a valid and realistic option. A few physical audits did take place, and to replace the traditional ‘shouting questions into the ear’ model of factory communication, many sites invested in headphones and radio sets to facilitate clearer discussions.
Video communications are moving as well; initially, meetings were desk bound, transferring the conversations from the office desk to the home office. But the possibility of connecting via smartphone has added the possibility of mobility. And if you can talk and move – well, you can move and work. As economies re-open, the positive habit of using smartphones while connected can be utilised to give real-time experiences and data – of factory and retail audits, of defect evaluations and of risk assessments.
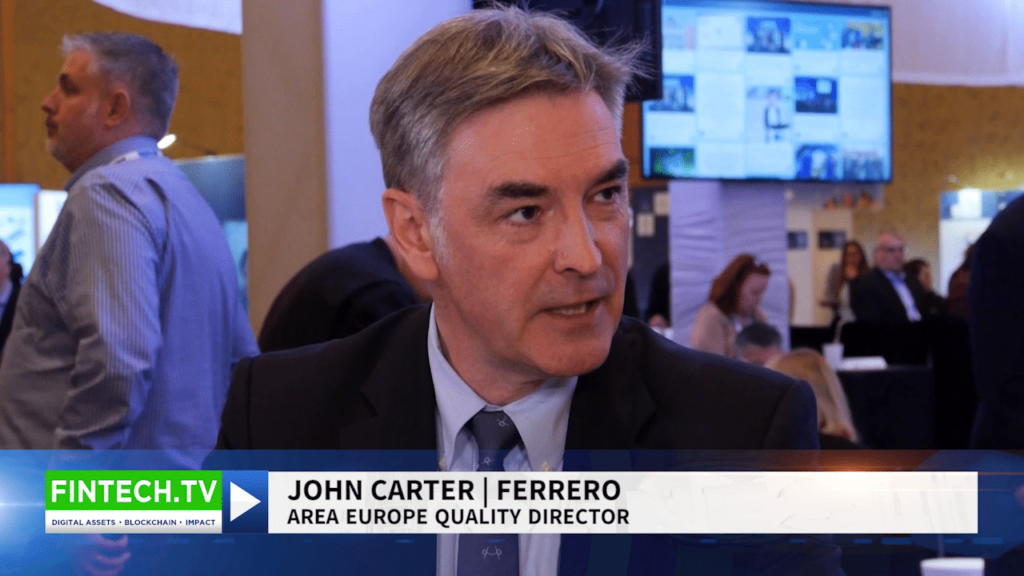
(you can also check out a very interesting interview he gave at FINTECH.TV during the GFSI 2020 event)
What do you do to address this need? What kind of tools and technologies do you use more?
Prior to this crisis, many observers, myself included, have commented on the opportunities offered by Big Data, both in the ability to know more about our supply chains and products and as a guarantor of traceability and transparency with technologies such as Blockchain.
My observations of the initial impact of Covid are that the effects have predominantly cultural and human – yes we have seen a huge rise in the use of video comms, documentation management (simplification) and workflow tools, but the main outcome has been to bring people closer together in collaborative teams.
There is certainly a need for reliable rapid analytical methods, for example, to assist in rapid decision making. But, at least for me, there has been an obvious need for human, rather than artificial intelligence. The same argument applies with supply chain technology – robust traceability, market intelligence and forecasting models needed human interpretation in this ‘black swan’ event to react logically to the external shock.
In other words, the first technological reaction to the constraints imposed by the crisis was tactical; enabling current processes rather than catalysing a step change. In a world where the pressure was on an industry to simply keep producing (“Feed the world! Just make it happen!”) we did not take the time to run pilot projects with new technology.
But now? Several months into the crisis, there is clear evidence of the strategic change that can be built on these new experiences, on this new culture of collaboration and fast decision making, and we can surely expect some major technological steps capitalising on the new reality.
Is there an area where digital technologies still fail to deliver? Where do you still see a need for more appropriate and efficient tools?
I think the answer is that we don’t yet know. There is a need for a review of what worked and what didn’t, and I think it is too early for one commentator to judge. We have proved as societies and teams that we are robust and connected, that we can continue to deliver under extraordinary pressure, that we can collaborate swiftly and supportively to do the right thing. Will Blockchain speed up those decisions? Do we need increased Cybersecurity to protect our data? What role can Artificial Intelligence play in the future? And, indeed, what is the future of work?
Any crisis presents both challenges and opportunities, and the advent of the global COVID-19 crisis has confronted the planet and the human race with both. In 2020, we have been given a glimpse of the future thanks to technology, and we now have a window of opportunity to enable positive change. Perhaps, indeed, we in the food industry have an obligation to use the human learnings of the crisis to deliver that change, because, after all… the production of food defines our world.